Download the case studies below to see how NaturalPave can work for you:
The environmentally positive road stabilization alternative from the innovators of soil stabilization technology.
NaturalPave Road Stabilization System
Midwest's NaturalPave Road Stabilization is an innovative stabilization system specifically designed to improve unpaved road performance, strength and longevity. The NaturalPave Road Stabilization consists of stabilizing the upper 4-8" of the existing road surface or in-place native soils with the option to include a selected surfacing technique that provides enhanced durability and all-weather traction while maintaining a natural aesthetic look. This system has also been studied by a third party and found to reduce carbon emissions, qualifying municipalities and counties to pursue federal funding for improving your gravel roads with NaturalPave.
NaturalPave Base Stabilization
NaturalPave® Base Stabilization is designed and installed to hold up to the most extreme traffic demands while maintaining a long service life. It is created by incorporating one of Midwest’s patented, environmentally friendly products into the existing soil or aggregate to create a strong, high performance base using the in-place material.
NaturalPave Surface
If desired, a specifically selected surface course is embedded into the surface of the NaturalPave Stabilized Base prior to the base curing. A variety of surface course options are available based on the traffic, desired look/aesthetics, performance/longevity and environmental considerations, among other things.
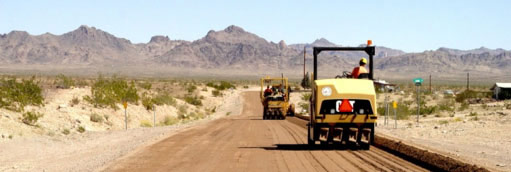
- Improved Bearing Strength
- Higher Loading Capacity
- Skid Resistant Surface
- Environmentally Friendly
- Easy to Maintain
- Weather Resistant
- Natural Looking Surface
- All Weather Traction
- Freeze-Thaw Resistance
- Visually Appealing
- Increased Fuel Efficiency
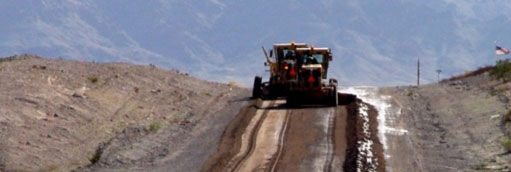
- Use of Local Materials
- Utilizes In-place Soils
- Cold Applied
- Long Installation Window
- Life Cycle Cost Savings
- Extended Service Life
- Easy Installation Process
- Reduced Surface Thickness
- Base Layer Design
- Limited Maintenance
- No Dust
FILL OUT THE FORM BELOW TO DISCOVER THE THIRD WAY.